서 론
우리나라의 산림면적은 2015년 기준 633만 ha에서 2050년에는 647만 ha로 증가할 것으로 전망하고 있는 반면 현재 국내 산림은 4영급(31~40년) 이상이 약 80% 이상으로 30년생 이상이 전체 산림면적의 72%를 넘어서기 때문에 벌목의 시기가 도래하였다 할 수 있다(Korea Forest Service, 2018; Korea Forest Service, 2021). 또한, 친환경 소재 선호에 따른 국내 목재 수요량은 지속적으로 증가할 전망이고(Korea Forest Service, 2018), 개도국의 원목 수출 금지정책과 수입목재 가격 상승 등 수입여건이 어려워져 국산 목재 생산에 대한 요구가 더 커지고 있다(Kim et al., 2015).
하지만 2019년 기준 178,419명의 임가인구 대비 산림작업 종사 가능 인력(20~59세 남자기준)은 29,216명(약 16.37%)으로 부족한 상황이며, 2050년에는 농산촌 인구가 2015년 대비 57.05%로 더 감소할 것으로 예측되고 있다(Korea Forest Service, 2018; Korea Statistical Information Service, 2020). 또한 작업의 기피현상과 노동임금의 급상승에 의해 목재의 생산성은 낮고 목재의 수요를 충당할 수 없는 실정이기 때문에 이러한 문제들을 해결하기 위해 고성능 임업기계의 도입이 필요하며 임업기계장비를 활용하여 벌채산물을 수집할 경우 인력대비 약 82%의 예산절감 효과와 8.4배의 작업능률 향상이 가능하다(Cho, 2015; Korea Forest Service, 2018). 이에 따라, 임업기계화의 추진이 시급히 요구되고 있으나 높은 숙련도의 작업원 부족, 작업시스템 구축의 미비 등으로 사업 추진이 원활히 진행되지 못하고 있는 실정이다(Kim et al., 2015).
국내에서 목재 생산을 위한 임업기계로써 굴삭기는 2016년 227대에서 2020년 278대로 22.4% 가량 보유가 많아졌으며, 비슷한 기구학적 모델을 갖는 포워더 또한 60대에서 70대로 16.7% 가량 보유가 많아졌다(Korea Forest Service, 2021). 대표적인 고성능 임업기계로써 하베스터와 포워더는 굴삭기의 매니퓰레이터나 너클 크레인 등에 엔드이펙터의 역할을 하는 수확기 헤드 또는 픽업 장치를 사용하여 필요한 작업을 수행한다. 수확기 헤드 또는 픽업장치를 작동시키기 전에 먼저 엔드이펙터를 목표물에 근접시켜야 하는데 이 때 각 매니퓰레이터를 동시에 조작해야 하므로 상당한 수준의 기술이 필요하다. 특히 산림 포워더를 이용한 크레인 작업은 목재 생산에 있어 가장 시간이 많이 걸리는 작업요소로 크레인 작업의 효율성을 높이는 것은 목재 생산성을 향상시키는데 필수적이다(Kellogg and Bettinger, 1994; Nurminen et al., 2006; Manner et al., 2016; Manner et al., 2017).
일반적으로 크레인은 조이스틱을 통하여 전기적 신호에 의해 한번에 하나의 액추에이터만 작동시킬 수 있으며, 엔드이펙터를 원하는 위치에 보내기 위해서는 각각의 액추에이터를 다축 조이스틱을 이용하여 동시에 제어해야 한다. 이는 교육과 오랜 시간동안 훈련을 거친 사람만이 구현할 수 있는 난이도가 매우 높은 기술이다. 크레인 팁 제어는 작업자가 엔드이펙터를 직관적으로 상하 또는 좌우로 이동시키는 방식으로 하나의 2축 조이스틱만을 사용하여 엔드이펙터를 독립적 또는 복합적으로 수평 및 수직제어를 수행한다. 이 기술은 크레인 조작의 기술적 난이도를 떨어뜨려 초보자도 쉽게 크레인 조작을 할 수 있을 뿐 아니라 숙련된 작업자도 작업 부하를 경감시켜 작업 생산성을 향상시킬 수 있다. 또한, 이 방식은 향후 자동제어가 가능한 방식으로 발전할 수 있고(Prorok, 2003; Chakraborty and Meena, 2016), 미국의 John Deere(2021)사는 2013년에 이러한 방식을 적용한 Intelligent Boom Control(IBC)이라고 하는 기술을 도입하였으며, 이 기술을 적용한 작업기를 이용하여 실제 운전자가 정확하게 크레인을 빠르게 제어할 수 있다고 소개하고 있다. 반면 국내의 연구는 작업기 헤드의 개발 정도로 특정 작업에 대한 편의성만 제공할 뿐 전체 크레인 작업을 위한 편의를 제공하기에는 미흡한 실정이다.
일반적으로 너클 붐 크레인은 RRRP(Revolute-Revolute-Revolute-Prismatic) 형태의 매니퓰레이터들을 갖고, 실린더의 직선운동을 통하여 각 조인트의 회전운동과 직선운동을 발생시켜 엔드이펙터를 제어한다. 너클 붐 크레인의 텔레스코픽(Telescopic) 실린더(RRRP중 P)를 제외한다면 굴삭기(RRR)의 형태와 같으며 두 기계 모두 슬류잉(Slewing) 기능(RRR 중 처음 R)은 수직 평면상에서 수평 및 수직경로를 제어하는 것과는 무관하며 공간상에서의 경로를 제어하는 역할을 하고 있다. 너클 붐 크레인의 텔레스코픽 실린더는 수직평면상에서 수평 및 수직이동의 범위와 관계가 있으며, 일정 범위 내에서는 붐 실린더와 암 실린더를 이용하고(RR 형태), 이동 중 일정 범위를 벗어나는 경우는 붐 실린더와 암 실린더, 텔레스코픽 실린더를 이용하여(RRP 형태) 수평 및 수직제어를 수행한다.
이러한 기계들을 구성하고 있는 실린더를 제어하기 위하여 사용되는 방법으로 PID 제어(P:비례, I:적분, D: 미분)는 각각의 계수를 구하기 위하여 시행착오적인 방식을 반복하게 되는데 부하나 유압오일의 불안정한 흐름, 유압오일의 온도 등과 같은 외란에 의해서도 움직임의 변화가 생길 수 있다. 이러한 이유로 계수를 정하는데 많은 시간이 걸리며 각각의 계수가 실험변수에 어떠한 영향을 끼치는지 알 수 없기 때문에 유압 실린더가 아닌 전기 모터를 사용하는 전동실린더를 사용할 경우 더 쉽게 제어가 가능하다(Prorok, 2003). 또한, 실린더를 제어하는데 있어 응답성이 우수한 장치를 사용하는 경우에는 빠른 제어주기만 유지한다면 단순 비례제어만으로도 충분한 제어가 이루어질 수 있다(Kim et al., 2009).
따라서, 본 논문에서는 전동실린더를 이용하여 크레인 구동이 가능한 실험실 규모의 기구물을 제작한 후 크레인에 대한 기구학 및 역기구학 해석을 통하여 크레인 팁의 기구학적 제어모델을 수립하고, 뱅뱅제어(Bang-bang control)을 통한 LBO 반경, 경로점의 개수, 실린더의 속도와 같은 적정 파라미터 선정을 거쳐 비례제어를 이용한 수직 평면상에서의 RR 매니퓰레이터에 대한 수평 및 수직경로 제어 알고리즘을 개발하여 그 성능을 평가하기 위하여 수행되었다.
재료 및 방법
국내 임업기계에서 대표적인 크레인 작업기로는 포워더가 있으며 본 연구에서는 실제 포워더의 크레인 작업기를 1/3 축소 스케일로 제작하여 전동실린더를 이용하여 제어가 가능하도록 하였다. 제작된 작업기는 텔레스코픽 기능이 구현되어 있지만 붐과 암실린더만을 이용한 일정 범위내에서의 수평 및 수직제어를 수행하는 알고리즘에 대한 실험을 진행함으로서 텔레스코픽 기능은 없는 것으로 가정하여 연구를 진행하였다(Figure 1). 사용된 전동실린더는 24V DC모터를 이용하여 ACME Screw를 통해 스트로크 제어가 가능한 모델이며 제원은 Table 1과 같다.
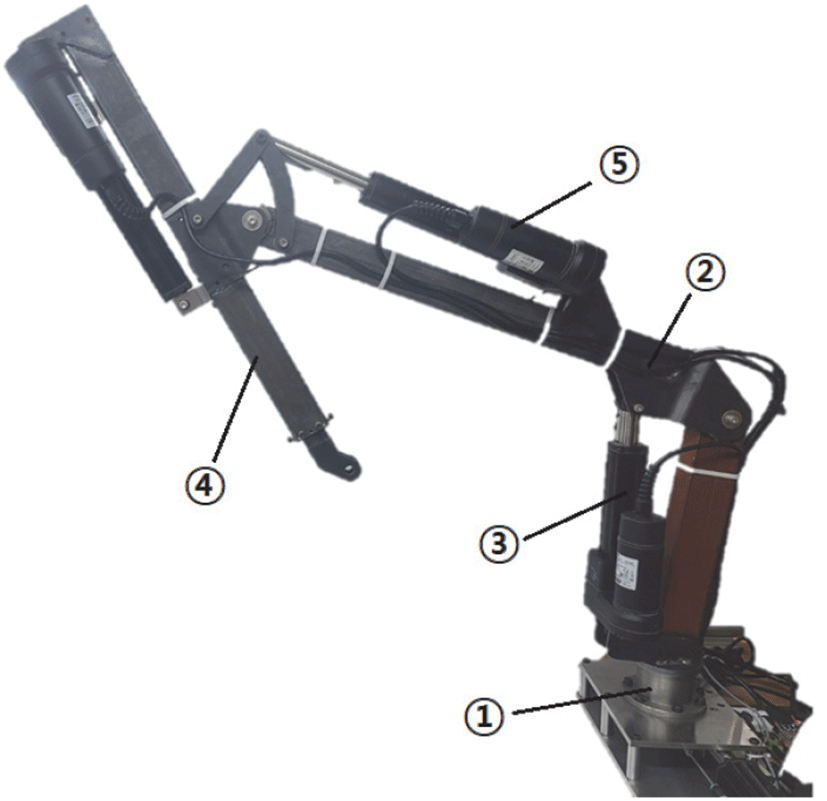
ECU(Electronic Control Unit)로 Arduino Due 보드를 사용하였으며, 각 축을 담당하는 서브 ECU들은 각각의 전동실린더에 부착된 아날로그 타입의 선형 거리센서의 값을 계측한 후, CAN(Controller Area Network) Bus를 통하여 메인 ECU로 전달된다. 메인 ECU는 전달받은 센서값을 이용하여 기구학적 분석 알고리즘을 거쳐 위치를 결정하기 위하여 시리얼 통신을 이용하여 DC 모터 드라이버에 명령을 전달하고, DC 모터 드라이버는 전달받은 명령을 통하여 PWM(Pulse Width Modulation)의 형태로 전동실린더를 동작시킨다(Figure 2).
Figure 3의 기구 해석을 위한 기구학적 특성을 규정하기 위하여 D-H 파라미터를 이용하였으며, 본 연구에서 제작된 크레인의 D-H 파라미터는 Table 2와 같다(Kim and Lee, 2007). O0는 슬류윙 조인트(Joint 0)로써 회전 조인트(Revolute Joint)이며, O1과 O2는 각각 붐과 암에 대한 조인트(붐 : Joint 2, 암 : Joint 3)로써 마찬가지로 회전 조인트이다. O3는 암과 붐을 연결함에 있어 기구적인 간섭을 방지하고자 생기는 상수 형태의 선형 조인트(Prismatic Joint)이며, O4는 최종 엔드이펙터까지의 거리를 나타내는 선형 조인트이다.
Joint i | θi | αi | di | ai |
---|---|---|---|---|
0(R) | 0 | 0 | 0 | 0 |
1(R) | θ1 | 90 | 422.2247 | -51.8427 |
2(R) | θ2 | 0 | 0 | 803.6246 |
3(P*) | θ3 | 90 | 0 | 59.5 |
4(P) | 0 | 0 | 412 | 0 |
where,
θi: the angle between xi − 1 and xi measured about zi, variable.
αi: the angle between zi and zi + 1 measured about xi, constant.
di: the distance from xi − 1 to xi measured along zi, constant.
ai : the distance from zi and zi + 1 measured along xi, constant.
*: fixed prismatic joint due to linkage.
순기구학은 각 조인트의 데이터를 이용하여 엔드이펙터의 위치를 알아내기 위한 방법으로 Figure 3과 같이 정의된 좌표계를 이용하였다. Joint 0를 기준으로 엔드이펙터인 크레인 팁의 위치는 식 1과 같이 각 조인트에서 변환 행렬의 곱이며, 로 표현할 수 있다.
여기서,
식 1에 D-H 파라미터값을 대입하면 식 2와 같이 표현될 수 있으며 Px, Py, Pz는 공간상에서의 좌표의 형태로 크레인 팁의 위치를 나타낸다.
여기서,
r11 = cosθ1 cos(θ2+θ3)
r12 = sinθ1
r13 = cosθ1 sin(θ2+θ3)
r21 = sinθ1 cos(θ2+θ3)
r22 = −cosθ1
r23 = sinθ1 sin(θ2+θ3)
r31 = sin(θ2+θ3)
r33 = −cos(θ2+θ3)
Px= −51.8427cosθ1+803.6246cosθ1cosθ2+59.5cosθ1 cos(θ2+θ3)+412cosθ1 sin(θ2+θ3)
Py= −51.8427sinθ1+803.6246sinθ1cosθ2+59.5sinθ1 cos(θ2+θ3)+412sinθ1 sin(θ2+θ3)
Pz= 422.2247+803.6246sinθ2+59.5sin(θ2+θ3)−412cos(θ2+θ3)
크레인의 슬류잉축은 회전축의 원점을 중심으로 공간상에서 움직일 수 있게 하며 독립적으로 제어가 되기 때문에 본 연구에서는 붐축과 암축만을 이용하여 각각의 조인트를 3° 간격으로 수직 평면상에서의 Py, Pz 좌표 형태로 작업 범위를 표현하였으며(The Math Works, inc., R2019b), 국가표준(KS B ISO:9283, 1998)에 따라 작업 범위 내에서 제어를 하기 위한 큐브를 설정(Figure 4)하고 그 중 조인트 각도 변화량에 따라 크레인의 팁 변화량이 큰 두 점((400, 400)에서 (1,000, 400))을 시작점과 끝점으로 설정하였다.
원하는 목표점으로의 제어를 위한 방법으로 시작점과 목표점, 두 점만을 이용한 크레인의 이상적인 제어 형태는 직선의 형태이지만, 기구적인 특성상 두 점만을 이용할 경우 붐 조인트와 암 조인트가 회전 운동을 하기 때문에 실제로 이루어지는 제어는 원을 그리는 형태로 나타나며 Figure 5와 같다.
따라서, Figure 6과 같이 시작점과 끝점 사이에 경로점(Waypoint)을 생성해서 원의 형태로 그려지는 실제 형상을 직선을 그리는 형태처럼 제어가 될 수 있도록 보완하였다.
불감대(Dead band) 영역이란 제어계에서 입력이 변화해도 출력이 발생하지 않는 입력의 범위로써 입력신호가 노이즈(Noise)와 같은 외란에 의하여 영향을 받을 경우 과도한 출력신호를 방지하고자 사용되는 방법이다. 본 연구에서 사용되는 붐 실린더와 암 실린더는 붐 조인트와 암 조인트의 회전을 목적으로 사용하기 때문에 각각의 각도를 기준으로 불감대 영역을 설정할 경우, 미세한 각도의 차이에 따라 목표점과 크게 오차를 가지며, 각각의 경로점에서 동일한 범위의 불감대 영역을 가질 수 없다(Figure 7, The Math Works, inc., R2019b).
따라서, 각 실린더의 각도를 기준으로 하지 않고 엔드이펙터의 목표 위치로써 공간상의 좌표인 경로점을 기준으로 경로점의 갱신 범위에 해당하는 LBO(Lateral Boundary Offset)를 적용하여 불감대 영역을 설정하였다(Figure 8, The Math Works, inc., R2019b).
적용한 LBO는 두 실린더를 이용하는 굴삭기 타입의 기구학적 모델의 특성상 경로점을 정확하게 통과하기 어렵기 때문에 불감대 영역으로써 적당하며 모든 경로점에 동일한 불감대 영역을 생성할 수 있다. 적용된 LBO의 범위는 식 6과 같이 표현되며, 반경(r)보다 작은 경우 다음 경로점을 목표점으로 갱신한다(Yoon, 2007).
여기서,
Py, current value : 공간상의 y축 현재 좌표
Py, target value : 공간상의 y축 목표 좌표(경로점의 y좌표)
Pz, current value : 공간상의 z축 현재 좌표
Pz, target value : 공간상의 z축 목표 좌표(경로점의 z좌표)
r : LBO의 반경(mm)
크레인 팁의 작업 범위 분석을 통하여 안정적으로 동작할 수 있는 임의의 범위[시작점(400, 400), 끝점(1,000, 400)]를 설정하였다. 적정 파라미터의 선정을 위하여 어떠한 계수에 의해 제어 성능에 영향을 끼치지 않는 단순 뱅뱅제어만을 적용하여 제어성능을 확인하였고, 실험변수로는 전·후진을 반복, LBO의 반경 2종류(5 mm, 7 mm), 경로점의 개수 3종류(20개, 30개, 40개)로 설정하여 각각 3회 반복 실험하였다. 매회 실험에서 항상 같은 시작점에서 출발하기가 어렵기 때문에 시작점의 위치에서도 LBO를 적용하여 범위 내에 허용이 되는 위치에서 실험을 진행하였다. 위치 정확도는 국가 표준(KS B ISO9283)의 자세 정확도를 참고하여 2차원일 경우를 적용해 원의 방정식을 이용하여 평균 오차를 산출하였고, 동작하는데 걸린 시간을 측정하였다. 추가적으로 실린더의 제어속도와의 관계를 확인하기 위하여 실린더 속도를 최대속도의 50%, 최대속도, 매 제어주기마다 변화하는 형태로 달리하여 위치 정확도와 소요시간을 확인하였으며, 매 제어주기마다 실린더의 속도가 변화하는 경우에는 뱅뱅제어가 아닌 비례제어를 적용하여 비례제어만을 이용한 제어 알고리즘을 적용할 수 있는지를 판단하였다. 비례제어를 적용하기 위해서 각각의 실린더에 대하여 전체 제어주기인 20 ms마다 듀티비(Duty ratio, 실린더 속도 입력)에 따른 실린더 변위량을 계측하여 전체 구간에 대한 관계식을 산출하였다(Figure 9).
산출된 관계식을 통하여 각각의 실린더는 매 제어주기마다 목표 위치와 현재 위치의 차이에 해당하는 듀티비를 출력하게 되는데 듀티비가 25% 미만일 경우에는 실린더가 움직이지 않기 때문에 산출된 듀티비가 25% 미만일 경우 최저 듀티비인 25%를 적용하여 정상상태 오차가 발생하지 않게 보정하였다.
현재 위치에서 임의의 목표 위치까지의 경로를 추종하는 경우 매 경로점마다 붐 실린더와 암 실린더의 변위는 기구학적 특성에 따라 달라지게 되며, 수평 경로제어의 경우 암 실린더의 변위가 붐 실린더의 변위보다 월등히 크다. 반대로 수직 경로제어의 경우에는 붐 실린더의 변위가 암 실린더의 변위보다 월등히 크며 이에 따라 두 실린더 중 하나의 실린더가 목표 위치에 먼저 도달하여 공간상의 좌표로써 오버슈트(Overshoot)나 언더슈트(Undershoot)가 발생하는 형태를 나타낼 수 있다. 따라서, 매 경로점마다 각 실린더가 동일한 시간동안에 목표 위치에 도착할 수 있도록 속도 게인(Gain)을 적용하여 상대적으로 변위가 작은 실린더를 느리게 움직이도록 하여 크레인 팁을 제어하기 위한 알고리즘을 개발하였다(Figure 10).
결과 및 고찰
전/후진별 LBO 반경과 경로점 개수에 따른 제어성능의 결과를 비교하였다(Table 3, Table 4).
LBO radius (mm) | No. of waypoints | Lead time (ms) | Error (mm) |
---|---|---|---|
5 | 20 | 8,460.000 | 17.976 |
30 | 14,726.667 | 12.915 | |
40 | 23,680.000 | 11.659 | |
7 | 20 | 5,973.333 | 19.888 |
30 | 8,580.000 | 14.521 | |
40 | 7,900.000 | 12.028 |
LBO radius (mm) | No. of waypoints | Lead time (ms) | Error (mm) |
---|---|---|---|
5 | 20 | 7,100.000 | 18.081 |
30 | 11,020.000 | 13.782 | |
40 | 18,046.667 | 11.732 | |
7 | 20 | 5,620.000 | 19.054 |
30 | 7,286.667 | 14.594 | |
40 | 10,033.333 | 13.635 |
전진을 할 경우, LBO 반경이 5 mm에서 7 mm로 증가함에 따라 경로점의 개수가 20개 일 때는 소요시간 8,460 ms에서 5,973 ms로 감소하였고, 평균 오차는 17.976 mm에서 19.888 mm로 증가하였다. 경로점의 개수가 30개 일 때는 소요시간은 14,727 ms에서 8,580 ms로 감소하였고, 평균 오차는 12.915 mm에서 14.521 mm로 증가하였으며, 경로점의 개수가 40개 일 때는 소요시간은 23,680 ms에서 7,900 ms로 감소하였고, 평균 오차는 11.659 mm에서 12.028 mm로 증가하였다. 후진을 할 경우, LBO 반경이 5 mm에서 7 mm로 증가함에 따라 경로점의 개수가 20개 일 때는 소요시간 7,100 ms에서 5,620 ms로 감소하였고, 평균 오차는 18.081 mm에서 19.054 mm로 증가하였다. 경로점의 개수가 30개 일 때는 소요시간은 11,020 ms에서 7,287 ms로 감소하였고, 평균 오차는 13.782 mm에서 14.594 mm로 증가하였으며, 경로점의 개수가 40개 일 때는 소요시간은 18,047 ms에서 10,033 ms로 감소하였고, 평균 오차는 11.732 mm에서 13.635 mm로 증가하였다. 전체적으로 전진과 후진 두 방향 모두 LBO 반경이 증가함에 따라 소요시간은 감소하고 평균 오차는 증가하는 경향을 나타내었고, 이는 LBO 반경이 증가함에 따라 실제 경로점까지 제어를 하지 않기 때문에 발생한 것으로 판단된다. 또한, 경로점의 개수가 증가함에 따라 소요시간은 증가하고, 평균 오차는 감소하는 경향을 나타내었으며, 이는 경로점의 개수가 증가함에 따라 더 많은 제어를 수행하기 때문에 발생한 것으로 판단된다.
각 조건별로 경로점의 개수와 LBO 반경에 대한 상관관계를 확인하고자 유의수준 5%에서의 이원배치 분산분석을 실시한 결과는 Table 5와 같다. 평균 오차의 경우 전진방향과 후진방향으로 이동할 때 경로점의 개수와 LBO 반경은 서로 간의 교호작용은 없고 각각 독립적으로 관계가 있는 것으로 분석되었고, 이를 통하여 평균 오차를 감소시키기 위한 독립된 변수로써 경로점의 개수와 LBO 반경을 각각 이용할 수 있을 것으로 판단된다. 소요시간의 경우 전진방향과 후진방향으로 이동할 때, 경로점의 개수와 LBO 반경 모두 관계가 있으며 서로 간의 교호작용이 있는 것으로 분석되었고, 이를 통하여 소요시간을 감소시키기 위해서는 경로점의 개수와 LBO 반경과의 상관관계를 규명하거나 독립된 다른 변수를 이용할 필요가 있을 것으로 판단된다.
전/후진별 LBO 반경과 경로점 개수에 따른 제어성능의 결과에서 평균 오차가 제일 작은 LBO 반경이 5 mm, 경로점의 개수가 40개인 경우를 선택하여 실린더 속도(최대속도의 50%, 최대속도, 매 제어주기마다 변화)에 따른 제어성능을 비교하고자 하였다(Table 6).
동일한 LBO 반경 조건에서 전진을 할 경우, 실린더의 속도가 50%에서 최대속도로 증가함에 따라 소요시간은 11,467 ms에서 23,680 ms로 증가하였고, 평균오차도 10.995 mm에서 11.659 mm로 증가하였다. 후진을 할 경우에는 실린더 속도가 50%에서 최대속도로 증가함에 따라 소요시간은 10,787 ms에서 18,047 ms로 증가하였고, 평균오차도 11.309 mm에서 11.732 mm로 증가하였다.
동일한 LBO 반경 조건에서 전진을 할 경우, 매 제어주기마다 속도를 변화하는 형태일 때의 소요시간이 9,080 ms로 가장 적었으며, 평균 오차는 11.210 mm로 확인되었다. 후진을 할 경우에는 매 제어주기마다 속도를 변화하는 형태일 때의 소요시간이 8,273 ms로 가장 적었고, 평균오차는 11.642 mm로 확인되었다.
실린더 속도와 평균 오차, 실린더의 속도와 소요시간에 대한 상관관계를 확인하고자 경로점의 개수는 40개, LBO 반경은 5 mm의 조건에서 유의수준 5%의 일원배치 분산분석을 실시한 결과는 Table 7과 같다. 평균 오차의 경우 실린더의 속도와 관계가 없는 것으로 분석되었고, 소요시간의 경우 실린더의 속도와 관계가 하나라도 있는 것으로 분석되었다. 따라서, 소요시간이 제일 작은 경우를 선택하여 설정한 경로점을 기준으로 전진을 할 경우와 후진을 할 경우의 크레인 팁의 제어 패턴을 확인하였으며, 전체적인 평균오차는 약 12 mm 이내이지만 목표점을 기준으로 오버슈트와 언더슈트를 반복하며 떨리는 형태로 제어가 이루어지고 있음을 확인하였다(Figure 11, Figure 12).
Parameter | Factor | SS | DF | MS | F | p |
---|---|---|---|---|---|---|
Forward | Error | 0.689 | 2 | 0.344 | 2.596 | 0.154 |
Lead time | 368.022 | 2 | 184.011 | 12.654 | 0.007 | |
Backward | Error | 0.298 | 2 | 0.149 | 3.267 | 0.110 |
Lead time | 154.542 | 2 | 77.271 | 98.611 | 0.000 |


전체적으로 전진과 후진 두 방향 모두 LBO 반경이 커짐에 따라 소요시간은 감소하고 평균 오차는 증가하는 경향을 나타내었고, 이는 LBO 반경이 커짐에 따라 실제 경로점까지 제어를 하지 않기 때문에 발생한 것으로 판단된다. 또한, 실린더의 속도가 증가함에 따라 소요시간과 평균 오차는 모두 증가하는 경향을 나타내었는데 통계분석의 결과로 평균 오차는 실린더의 속도와는 관계가 없지만 실린더가 빠른 속도로 움직일 때 실린더의 관성력으로 인하여 경로점의 범위를 벗어나는 오버슈트 또는 언더슈트 현상이 발생하기 때문에 경로점으로 수렴하기 위한 시간이 더 소요되었을 것이고 그 사이 생기는 누적오차에 의하여 평균오차도 증가하였을 것으로 판단된다. 따라서, 이를 보완하기 위하여 매 제어주기마다 실린더의 속도를 변화시키는 비례제어 알고리즘을 적용하였을 때에는 소요시간이 큰 폭으로 줄어드는 경향을 확인하였지만, 제어 패턴은 경로상에서 오버슈트와 언더슈트 현상이 많이 발생하고, 이는 경로점으로 도달할 때의 붐 실린더의 변위량과 암 실린더의 변위량의 차이가 있어 두 실린더 중 하나의 실린더가 먼저 목표 위치에 도착해서 발생한 것으로 판단된다.
붐 실린더와 암 실린더를 제어함에 있어 각각의 실린더가 동일한 시간동안 목표 위치에 도달하게 하기 위한 속도 게인을 적용한 크레인 팁 제어 알고리즘을 개발하여 LBO 반경이 5 mm인 조건에서 전/후진별 소요시간과 평균오차를 확인하였다(Table 8).
Direction | Lead time (ms) | Error (mm) | ||||||
---|---|---|---|---|---|---|---|---|
1st | 2nd | 3rd | Average | 1st | 2nd | 3rd | Average | |
Forward | 5,360 | 5,340 | 5,320 | 5,340 | 10.253 | 10.233 | 10.233 | 10.240 |
Backward | 5,200 | 5,220 | 5,180 | 5,200 | 10.099 | 9.911 | 10.108 | 10.039 |
최종적으로 속도 게인의 형태를 적용한 크레인 팁 제어 알고리즘은 기존에 적용되지 않은 제어형태와 큰 차이가 있음을 확인하였다. 전진의 경우, 평균 소요시간은 9,080 ms에서 5,340 ms로 약 1.7배 정도 빨라졌으며, 평균오차는 11.210 mm에서 10.240 mm로 약 8.65% 감소하였다. 후진의 경우에는 평균 소요시간이 8,273 ms에서 5,200 ms로 약 1.6배 정도 빨라졌으며, 평균오차는 11.642 mm에서 10.039 mm 약 13.77% 감소하였다.
평균오차의 경우에는 LBO의 반경에 영향이 크기 때문에 실제로 제어가 이루어지는 형상을 확인하였다(Figure 13, Figure 14). 속도 게인을 적용하지 않은 경우에는 Pz축 375 ~ 425 mm 범위 내에서 오버슈트와 언더슈트를 반복하며 제어가 이루어졌지만 속도 게인을 적용한 크레인 팁 제어 알고리즘의 경우 Pz축 395~405 mm 범위 내에서 제어가 이루어짐을 확인하였다. 추가적으로 동일한 조건에서 수직제어의 경우에는 Py축 740~760 mm 범위 내에서 제어가 이루어짐을 확인하였다(Figure 15, Figure 16).


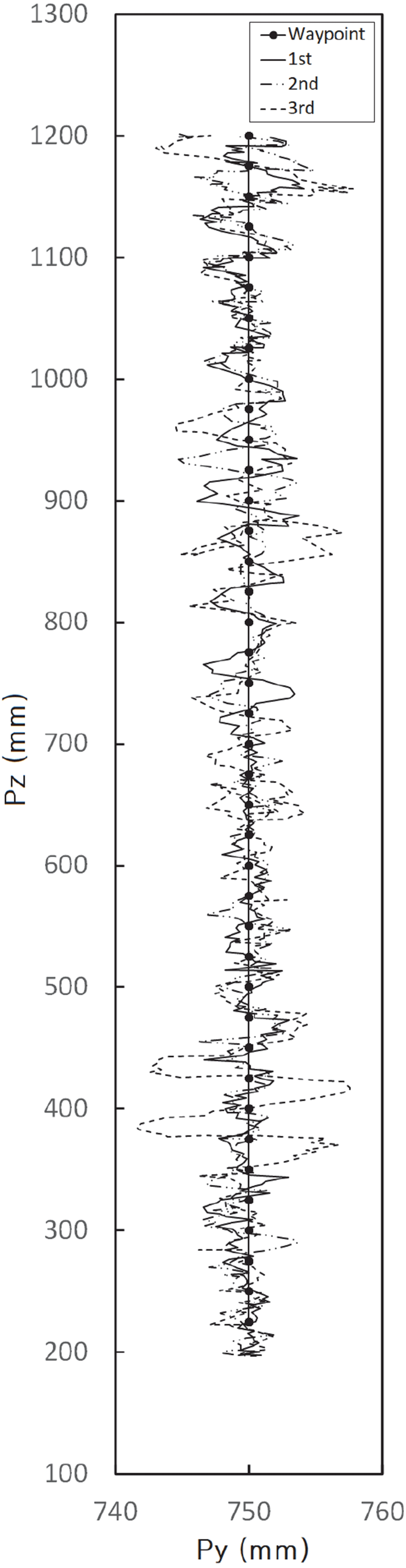
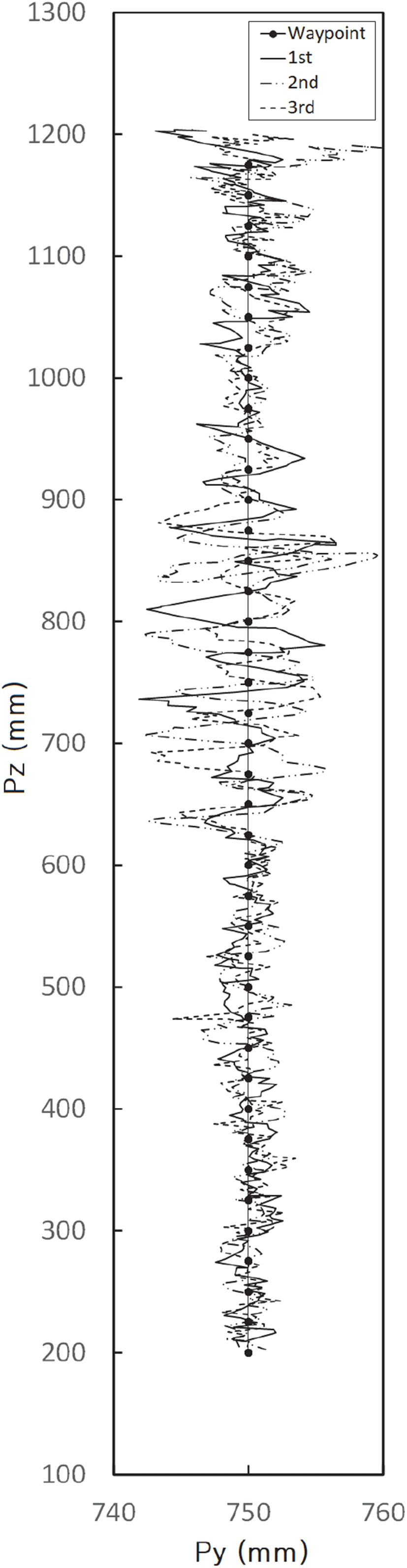
따라서, 크레인 팁을 제어하기 위해서는 기구적인 특성으로 인하여 생기는 두 실린더 간의 변위를 동일한 시간에 제어가 이루어질 수 있도록 속도 게인을 적용하고, 제어주기 20 ms에서 단순 비례제어만을 이용할 수 있을 것으로 판단된다. 본 연구에서는 아날로그 타입의 선형 거리센서를 이용하여 수행이 되어 기계의 떨림이나 노이즈의 영향으로 LBO 반경이 5 mm 미만에서의 실험을 진행하지 못하였지만 디지털 타입의 센서를 이용하여 노이즈의 영향을 줄인다면 적정 LBO 반경을 더 줄일 수 있고, 그에 따른 경로점의 수가 증가하기 때문에 동일한 알고리즘을 적용하였을 때 평균오차가 더 작아지는 결과를 가져올 것으로 예상된다.
결 론
고성능 임업기계인 하베스터 또는 포워더 등에서의 크레인 부 운전 조작은 다수의 조이스틱을 복합적으로 제어해야 하는 고난이도의 기술이 필요하다. 하나의 조이스틱으로 직관적인 직선운동을 수행할 수 있는 임업용 크레인 팁 제어 시스템을 개발함에 있어 하베스터로 사용하는 굴삭기에도 적용하기 위하여 크레인의 텔레스코픽 기능을 없다고 가정하고 RR 매니퓰레이터에 대한 기구학적 모델 기반의 제어 시스템을 개발하여 전동실린더로 구동되는 실험실-규모의 크레인을 제작하여 제어성능을 평가하였다.
이동 목표지점까지의 전체 경로에 다수의 경로점을 두어 크레인팁이 이 경로점들을 추종하는 경로추종 제어알고리즘이 적용되었으며 제어 파라미터 선정을 위하여 뱅뱅제어를 이용하여 LBO 반경과 경로점의 개수, 실린더의 속도에 따른 제어성능을 확인하였다. LBO 반경이 증가함에 따라 제어 소요시간은 감소하고 평균 오차는 증가하는 경향이 나타났으며 경로점의 개수가 증가함에 따라 소요시간은 증가하고 평균 오차는 감소하는 경향이 나타났다. 통계분석의 결과로 평균 오차를 감소시키기 위한 독립된 변수로써의 경로점의 개수와 LBO 반경은 경로점 사이의 거리가 LBO 직경보다 작지 않은 선에서 하나의 식으로 도출될 수 있을 것으로 판단되며, 소요시간을 감소시키기 위해서는 경로점의 개수와 LBO 반경과의 교호작용이 있기 때문에 독립된 변수를 찾아야 할 것으로 판단되었다. 추가적인 실험을 통하여 실린더 속도가 감소함에 따라 소요시간과 평균 오차는 모두 감소하는 것을 확인하였으며, 실린더의 속도는 소요시간을 감소시키기 위한 독립된 변수임을 검증하였다. 또한, 비례제어를 적용하여 매 제어주기마다 실린더의 속도를 변화할 경우 소요시간이 큰 폭으로 감소하는 경향을 확인하였지만 실제 제어의 형상을 확인하여 큰 범위에서 오버슈트와 언더슈트를 반복하며 제어가 이루어 짐을 확인하였다. 따라서, 추가적으로 각각의 실린더의 속도를 상대적으로 변경할 수 있는 속도 게인을 적용해야 할 것으로 판단하였고, 최종적으로 속도 게인이 적용된 비례제어만을 이용한 크레인 팁 제어 알고리즘을 개발하여 성능을 분석하였다.
개발된 알고리즘은 전/후진의 결과 모두 약 10 mm의 평균 오차를 가졌고 실제 제어의 형상은 속도 게인이 적용되지 않았을 때보다 약 5배정도 오차가 감소된 범위 내에서 제어가 이루어짐에 따라 20 msec의 제어주기에서 속도 게인이 적용된 비례제어만을 이용하여 크레인 팁 제어가 가능한 것으로 검증되었다. 향후, 동일한 제어 방식을 적용하여 슬류잉 기능과 텔레스코픽 기능에 대한 추가 연구를 진행하여 시스템을 개발할 경우, 공간상에서 직관적인 움직임을 갖는 고성능의 임업기계로써 하베스터와 크레인에 모두 적용이 가능할 것으로 보이며, 더 나아가 자동제어까지 가능한 시스템을 개발할 수 있을 것으로 판단된다.