서 론
전 세계적으로 증가하는 에너지 수요와 화석 연료의 온실가스(GHG, GreenHouse Gas) 배출 증가에 따른 부정적 영향에 대한 우려로 저비용이고 재생 가능하며, 환경오염이 없는 대체 에너지자원이 필요한 실정이다(Smeets and Faaij, 2007; Fililppou et al., 2018). 특히 벌채부산물은 미이용 산림바이오매스로써 효과적으로 생산·이용할 경우 에너지원으로서의 잠재력이 크다. 그러나 벌채부산물 연료는 수집과정에서 많은 광물질과 오염물질을 포함할 수 있으며, 이는 에너지연료로 활용시 연소에 부정적인 영향을 미칠 수 있다(Gendek and Zychowicz, 2015; Gendek and Malat’ák, 2018). 대부분 벌채부산물로 생산된 에너지 연료는 국제표준(함수율, 회분)을 충족하지 않고, 중소 규모 에너지 플랜트나 연소 시스템에 기술적인 문제(유해가스 배출, 효율 저하, 시스템 작동 오류)가 발생할 수 있다(Euh et al., 2014; Moskalik and Gendek A, 2019). 또한, 벌채부산물을 에너지로 이용하기 위해서는 작업효율과 연료의 품질 향상을 목표로 공급하여야 하며, 연소조건은 에너지 플랜트의 요구사항(크기, 함수율, 회분)을 충족해야한다(Gendek and Nawrocka, 2014; Gendek and Nurek, 2016).
국내는 대부분 단목수확시스템(CTL, Cut-to-length harvesting system)이며, 체인톱을 이용한 벌도 및 조재작업, 굴삭기 우드그랩(자체중량 5톤, 버킷 크기 0.2 m3)를 이용한 집재작업, 임내차를 이용한 소운반 작업으로 이루어진다(Lee et al., 2019). 굴삭기 우드그랩를 이용한 집재작업(Shovel logging)은 조림작업을 위해 벌채부산물을 모으는 정리작업, 벌도 및 조재된 원목과 벌채부산물을 동시에 임도변이나 토장으로 내려 작업을 실시한다. 이러한 과정에서 임지훼손 문제나 토양과 이물질 등이 포함되어 목재제품의 손상 및 가치가 하락하게 된다(Kim and Park, 2012; Lee et al., 2016; Lee et al., 2019). 그러나 최근 미이용 산림바이오매스(벌채부산물)의 신재생에너지 공급인증서(REC: Renewable Energy Certificate)가 개정되고, 경제적 가치가 없어 임지에 방치되었던 벌채부산물이 톤당 68,000원∼70,000원으로 거래되면서 수집 및 이용을 위한 임업시장이 변화하고 있다(Cho, 2019). 이에 따라 열에너지 연료용으로 사용하기 위한 목재칩의 형태는 목재 연료칩(Wood chips fuel)과 호그(Hog fuel)로 구분되고, 국내에서 원목이나 벌채부산물로 생산된 목재칩을 이용한 열발전 시설에서 요구되는 중요한 인자로 크기, 회분 함량과 함수율 등이 연소시설에서 영향을 미치며, 이를 향상 시키기 위한 방법으로 별도의 선별작업과 건조 비용 등이 발생 될 수 있다. 이러한 문제점을 해결하기 위해 벌채부산물 목재칩을 경제적으로 생산할 수 있는 방법과 에너지로서 가치를 증대하고 이를 활용하기 위해 목재칩의 특성(물리적 및 화학적 특성) 분석을 통해 품질 향상에 관한 연구가 필요한 실정이다.
국내·외 선행연구를 살펴보면, 미국 및 유럽 등에서는 원목과 벌채부산물을 효율적으로 생산하기 위해 단목 및 전목수확시스템(WT, Whole-tree harvesting system)을 이용한 생산성과 비용 연구를 통해 전목수확시스템이 경제적으로 더 유리한 것으로 보고되었다(Adebayo et al., 2007; Spinelli and Magagotti, 2010). 국내도 단목 및 전목수확시스템에 대한 연구가 일부 진행되었으며, Kim and Park(2012, 2013)은 단목 및 전목수확시스템에서 비용이 오히려 전목이 37.4% 높게 나타났고, Cho et al.(2019)은 전목수확시스템 비용이 단목보다 1.6%으로 비교적 낮게 절감된 것으로 나타났다. 이러한 원인으로 국내는 전목수확시스템을 적용할 수 있는 인프라가 구축되어 있지 않고 굴삭기 우드그랩을 이용한 집재방식이 비용적으로 낮기 때문에 지금까지도 단목수확시스템을 이용한 원목 및 벌채부산물을 수집 및 이용하고 있다.
최근 유럽에서는 벌채부산물 연료를 경제적이고 품질을 향상시키기 위한 방법으로 다양한 목재파쇄기(형태, 동력 성능, 칼날, 스크린 크기)를 대상으로 효율적인 연료용 목재칩 생산에 관한 연구가 진행되었다(Nati et al., 2010, 2014; Eliasson et al., 2015; Spinelli and Hartsough, 2001; Spinelli and Visser, 2009). 또한 선별작업에 따른 연료용 목재칩 품질(함수율, 크기, 발열량, 회분) 향상을 위해 선별기의 스크린 종류별(데크, 스타스크린) 생산성, 비용 및 연료특성을 비교·분석하였다(Laitila and Nuutinen, 2015; Woo, 2015; Huber et al., 2017). Kuptz et al.(2019)는 선별 및 건조 작업을 통해 소규모 바이오매스 보일러(<100kW)에 적합한 목재칩의 등급을 향상시키는 연구를 수행하였다. Pollex et al.(2020)는 목재 가스화 플랜트(Wood gasification plant)를 대상으로 저급 목재칩 품질(함수율, 미세분 감소)을 향상시켜 연소 후 발생된 가스를 열병합 발전(CHP, Combined heat and power)에 이용하여 효율(열, 전기)을 증가시킬 수 있는 연구를 수행하였다. 또한 벌채부산물 연료를 수요처(에너지 이용시설)에 고려하여 공급하기 위한 수확방법, 원산지 및 공급원, 크기, 함수율, 회분, 겉보기 밀도, 발열량, 원소분석 등의 국제표준에 따른 연료 등급 분류에 관한 연구가 진행되었다(Nordhagen, 2014; Filippou et al., 2018; Moskalik and Gendek, 2019). 이에 국내도 벌채부산물을 이용한 목재칩 연료에 관한 연구로 목재파쇄기(형태, 동력성능)를 이용한 생산성과 비용, 목재칩의 물리적 특성(크기, 함수율)에 대해 일부 연구가 수행되었다(Cha et al., 2011; Choi et al., 2019). 또한 국내는 벌채부산물 목재칩 연료를 대상으로 열 및 전기를 생산할 수 있는 에너지 이용시설을 확대하고 있으며, 2020년 목재칩 등급을 상향 개정하면서 품질 향상 요구도가 높아지고 있다(NIFoS, 2020). 그러나 국제표준(ISO 17225-4:2021) 기준 등급 분류 항목 중 회분, 원소, 무기물에 대한 국내의 목재칩 등급 기준(이하 NIFoS 제2020-2호, NIFoS, 2020)이 허용 범위가 넓기 때문에 에너지 이용시설에 적합한지 검토가 필요하다. 이를 통해 수요처를 고려한 목재칩 공급과 품질 향상을 위한 수확방법, 파쇄작업, 선별작업, 연료 등급 분류를 통해 에너지 이용시설에서의 적합성과 이용 가능성에 관한 연구는 미흡한 실정이다. 따라서 본 연구목적은 단목 및 전목수확시스템에서 발생하는 벌채부산물을 에너지 연료로 이용하기 위한 생산·가공에서 생산성 및 비용을 비교 분석한다. 또한 목재수확방법에 따라 생산된 연료용 목재칩의 연료 특성 및 등급 분류를 통해 에너지 이용시설에서의 적합성과 이용 가능성을 검토하고자 하였다.
재료 및 방법
본 연구 대상지는 낙엽송 수종으로 모두베기 작업지인 가평군 조종면 운악리 산 134-1번지(37°54′40.0″N 127°19′53.6″E, 단목수확시스템)와 강원도 춘천시 서면 덕두원리 산 183-7번지(37°53′41.5″N 127°37′29.2″E, 전목수확시스템)로 목재수확 후 발생된 벌채부산물을 수집하였다(Figure 1). 연구대상지의 지황 및 임황은 Table 1과 같다.
단목수확시스템은 국내에서 가장 많이 이용하는 방식으로 원목은 임지 내에서 체인톱(5200, ZENOAH, Japan; 372XP, HUSQVARNA, Sweden)을 이용한 벌도 및 조재작업, 5톤급 굴삭기 우드그랩(DX55, DOOSAN, Korea)을 이용한 집재작업, 궤도형 임내차와 5톤급 굴삭기 우드그랩을 이용한 소운반 작업, 카고트럭과 5톤급 굴삭기 우드그랩을 이용한 운송작업을 실시하였다. 벌채부산물은 5톤급 굴삭기 우드그랩(DX55, DOOSAN, Korea)을 이용한 수집작업, 차륜형 임내차(영운기, 군용트럭 개조차량)와 5톤급 굴삭기 우드그랩을 이용한 소운반 작업을 실시하였고, 토장에서 파쇄현장으로 상차 및 운송하기 위해 5톤급 굴삭기 우드그랩과 25톤 암롤트럭을 이용하여 수집하였다(Figure 2).
전목수확시스템은 지상집재(완경사지)와 가선집재(경사지) 작업으로 구분된다. 본 연구대상지는 가선집재방식을 적용하였으며, 평균 경사가 31.4%로 굴삭기 기반의 하베스터(25SH, KESLA, Finland)를 이용하여, 벌도작업을 실시하였고, 굴삭기 기반의 타워야더(SW-200, HSM, Korea)를 이용한 집재작업, 굴삭기 기반의 프로세서(Woody60, KONRAD, Austria)를 이용한 조재작업을 실시하였다. 전목수확시스템의 경우 단목수확시스템과 달리 소토장이나 임도변에서 조재되어 별도의 벌채부산물 수집작업이 필요하지 않다. 이에 벌채부산물은 굴삭기 우드그랩과 차량형 임내차를 이용한 소운반 작업을 실시하였고, 토장에서 파쇄현장으로 상차 및 운송하기 위해 5톤급 굴삭기 우드그랩과 5톤 카고트럭을 이용하여 수집하였다(Figure 3).
벌채부산물을 목재칩으로 생산하기 위해 사용한 파쇄기계는 드럼형 목재파쇄기(C645T, KESLA, Finland)로 203마력급 임업용 트랙터(203T, VALTRA, Finland)의 동력인출장치(PTO, Power Take-Off)에 의해 작동되며, 자체 크레인에 로그 그래플이 장착되어 있다. 목재파쇄기의 드럼 직경은 570 ㎜이며, 드럼에 장착된 파쇄칼날은 좌측날 3개, 우측날 3개 총 6개로 구성되어있다. 또한 목재칩 크기를 조정할 수 있는 스크린이 장착되어 있으며, 수요처에서 요구하는 목재칩 크기(40 mm)를 고려하여 파쇄작업을 실시하였다.
단목 및 전목수확시스템에서 벌채부산물의 생산 및 가공처리에 따른 생산성 분석을 위해 스톱워치를 이용한 시간 및 동작연구(Time and motion study) 방법을 적용하였다(Cho et al., 2018; Choi et al., 2018; Cho et al., 2019). 벌채부산물 수집 생산량의 경우 소운반과 운송작업 시 트럭스케일(RW-10T, CAS, Korea)를 이용하여 측정하였다. 목재칩 생산량의 경우 컨테이너 크기 14 m3을 가득 채워 파쇄한 후 트럭스케일을 이용하여 중량을 측정하였고, 선별량은 각 토출부에 톤백마대를 설치하여 미세칩(Fines), 유효칩(Accept), 초과칩(Over) 등을 구분하여 중량을 측정하였다. 또한 벌채부산물 수집 및 목재칩 생산·가공작업에서 임업기계의 기계비용 산출에 필요한 인자로 장비구입가격, 내구년수, 연간작업시간, 유류소비량, 유류단가, 수리 및 유지비, 이자율, 인건비 등을 조사하였다.
국내는 대부분 원목과 벌채부산물를 동시에 같이 수집하기 때문에 각각의 시간비율(원목 54.4%, 벌채부산물 45.6%)을 고려하여 수집 생산성을 분석하였다. 목재칩 파쇄 및 선별작업 생산성은 전체작업시간(Cycle time), 순수작업시간(Delay-free cycle time) 및 작업지연시간(Delay time)으로 구분하여 기계이용률(Utilization, %)을 산출하였다. 작업생산성(m3/SMH; Scheduled Machine Hour)은 전체작업시간(SMH)과 전체작업량(Gwt, Green weight ton)으로 분석하였다. 또한 소운반과 운송작업 생산성(Gwt/day)은 회당 소요시간과 적재중량(Gwt, Green weight ton)을 이용하여 분석하였다.
작업비용(won/Gwt)은 다음 식 1과 같이 기계비용(won/ SMH)과 작업생산성(Gwt/SMH)을 이용하여 산출하였다.
기계비용은 Table 2와 같이 독일 산림작업 및 임업기계위원회(KWF, Kuratorium für Waldarbeit und Forsttech nik e. V)에서 정한 방식으로 감가상각비, 이자비, 수리 및 유지비, 유류비, 인건비 등을 이용하여 산출하였다(Miyata, 1980; Woo et al., 1990; Brinker et al., 2002; Choi et al., 2018; Cho et al., 2019). 소운반작업에 경우 사용된 장비는 차륜형 임내차(영운기)로 군용 트럭을 개조하여 사용되고 있으며, 기계비용을 산출하는 인자값 조사가 어려운 관계로 국내 원목생산업자을 대상으로 탐문조사를 통해 1일 기준 단가(450,000 won/day)를 적용하였다. 또한 벌채부산물 운송작업은 단목수확시스템의 경우 25톤 트럭, 전목수확시스템은 5톤 트럭을 이용하였고, 각각의 운송거리는 90 km와 40 km이었다. 이는 거리와 장비가 다르기 때문에 비교하기에 다소 무리가 있을 것으로 판단하여 선행연구(Cho, 2019) 결과를 바탕으로 평균 거리에 가장 근접한 100 km 기준을 적용하여 분석하였다.
a 174 day × 8 hour=1,392 hours (Korea Forest Service, 2012)
b Endurance period (Miyata, 1980; Woo et al., 1997; Brinker et al., 2002)
단목 및 전목수확시스템의 벌채부산물 목재칩 선별처리에 따른 등급 분류를 비교하기 위해 국제표준과 국내기준에서 고시한 목재제품의 규격과 품질 기준(목재칩)으로 목재칩 크기(Particle size), 겉보기 밀도(Bulk density), 함수율(Moisture content), 회분(Ash content), 원소(Elementary), 무기물(Inorganic substances), 발열량(Heating value) 등의 항목을 조사·분석하였다.
목재칩의 시료 채취 방법은 파쇄작업이 완료된 후 적재함에서 앞, 중간, 뒤 부분에서 최소 3개의 종이백과 20 ℓ 지퍼마대를 이용하고, 원추형 4분법을 적용하여 시료를 채취하였다. 목재칩의 겉보기 밀도는 적재함 14 m3(Length 4.5 m×Width 2.2m×Height 1.4 m)을 기준으로 목재파쇄기에서 직접 분사하여 적재함을 가득 채운 상태에서 트럭 스케일로 중량을 측정하였다. 또한, 목재칩의 함수율은 파쇄작업 후 채취한 시료를 건조기(LBV-100, Jeio Tech Co., Korea)에 넣어 105 °C에서 24시간 건조 후 저울(XB4200HX, CAS Co., Korea)을 이용하여 무게를 측정하였다(ISO 18134-1). 목재칩의 크기는 ISO 3310-2 기준에 의해 3.15 mm, 8 mm, 16 mm, 31.5 mm, 45 mm, 63 mm 등으로 구분하였고, 시험방법은 ISO 17827-1에 의하여 시험 중 입자 간의 붙는 현상을 제거하기 위해 습량 기준 함수율이 20% 이하가 되도록 조절하였고, 진동체 선별기(RP-10, CISA Co., Spain)를 이용하여 분류 후 저울로 중량을 측정하였다.
회분 측정은 ISO 18122 시험법을 이용하여 빈 도가니의 무게를 측정한 후 약 1 g의 샘플을 정칭하여 담고 회분 분석기를 통해 측정하였다. 발열량을 측정하기 위해 ISO 18125 시험법을 이용하여 시료를 채취하고 105 °C 오븐에서 약 3시간 건조한 후 무게를 측정하고 발열량(Parr 6400, Parr Instrument Company, USA) 분석기에 투입하여 분석하였다. 원소 분석은 국제표준과 국내기준에서 동일한 질소(ISO 16948), 황, 염소(ISO 16994) 항목을 고시된 시험법을 통해 분석하였다. 또한 무기물 분석 항목 중 비소, 카드뮴, 크롬, 납, 수은은 국내와 국제표준과 동일한 분석항목이나 국제표준에서는 구리, 니켈, 아연 등이 추가적인 항목에 있으나 벌채부산물를 원료로 하는 목재칩 대상에서는 분석이 요구되지 않고 국내기준은 모든 원료에 분석이 필요하기 때문에 고시된 ISO 16968 시험법을 통해 측정 및 분석을 실시하였다.
결과 및 고찰
단목수확시스템에서 벌채부산물 목재칩의 생산·가공작업 생산성은 운송작업(14.5 Gwt/SMH), 파쇄작업(11.6 Gwt/ SMH), 선별작업(7.7 Gwt/SMH), 소운반작업(7.3 Gwt/SMH), 수집작업(5.0 Gwt/SMH) 순으로, 높게 나타났으며 시스템 생산성은 1.6 Gwt/SMH로 분석되었다. 작업비용은 총 89,865 won/Gwt이며, 운송작업비용이 24,725 won/Gwt로 가장 높았으며, 수집작업비용이 13,975 won/Gwt로 가장 낮은 것으로 산출되었다. 전목수확시스템에서 벌채부산물 목재칩의 생산·가공작업 생산성은 운송작업(14.5 Gwt/SMH), 파쇄작업(14.3 Gwt/SMH), 선별작업(7.7 Gwt/SMH), 소운반작업(7.1 Gwt/SMH) 순으로 높게 나타났으며, 시스템 생산성은 2.9 Gwt/SMH로 분석되었다. 작업비용은 총 72,974 won/ Gwt이며, 운송작업비용이 24,725 won/Gwt로 가장 높았으며, 파쇄작업비용이 14,999 won/Gwt으로 가장 낮았다. 또한 단목과 전목수확시스템에서 소운반 및 파쇄작업 생산성과 비용 차이는 각각 연구대상지의 임지조건이 다르며, 소운반 거리가 전목수확시스템이 0.8 km가 더 높아 생산성이 낮고 비용이 높은 것으로 나타났다. 파쇄작업은 벌채부산물을 수집 및 운송하여 파쇄작업을 하기 전 노지에 보관시기가 서로 달라 함수율에 대한 영향으로 생산성과 비용에서 차이가 발생한 것으로 나타났다(Table 3).
d Transportation distance : 100 km (25ton truck)[Cho. 2019],
선행연구에서 단목 및 전목수확시스템을 이용한 생산성과 비용 연구에서 전목수확시스템이 생산성이 높고 비용은 절감되는 것으로 나타났고(Adebayo et al. 2007; Spinelli and Magagotti, 2010), 특히 Cho et al., (2019)의 선행연구에서 유사한 연구결과로 전목수확시스템에서 가선집재장비와 프로세서를 이용한 원목생산을 집하장에서 실시하는 것으로 별도의 수집비용이 발생하지 않기 때문에 비용이 절감되는 것으로 나타났다. 따라서 단목수확시스템에서 전목수확시스템으로 전환하였을 때 작업비용을 18.7% 절감할 수 있을 것으로 판단된다.
단목 및 전목수확시스템의 벌채부산물 목재칩 선별처리에 따른 크기 분석은 Figure 4와 같다. 선별작업을 통해 단목과 전목수확시스템의 벌채채부산물 유효칩의 비율이 증가되었으며, 미세분 비율이 감소되는 것으로 나타났다. 단목수확시스템의 벌채부산물 목재칩은 선별하여 유효칩이 9.6% 향상되었고, 미세분이 98.5% 감소되었다. 전목수확시스템의 경우 선별하여 유효칩이 11.4% 향상되었고, 미세분은 96.6% 감소되었다. 그러나 선별유무에 따른 모든 목재칩에서 미세분을 제거할 수 없는 것으로 나타났다.
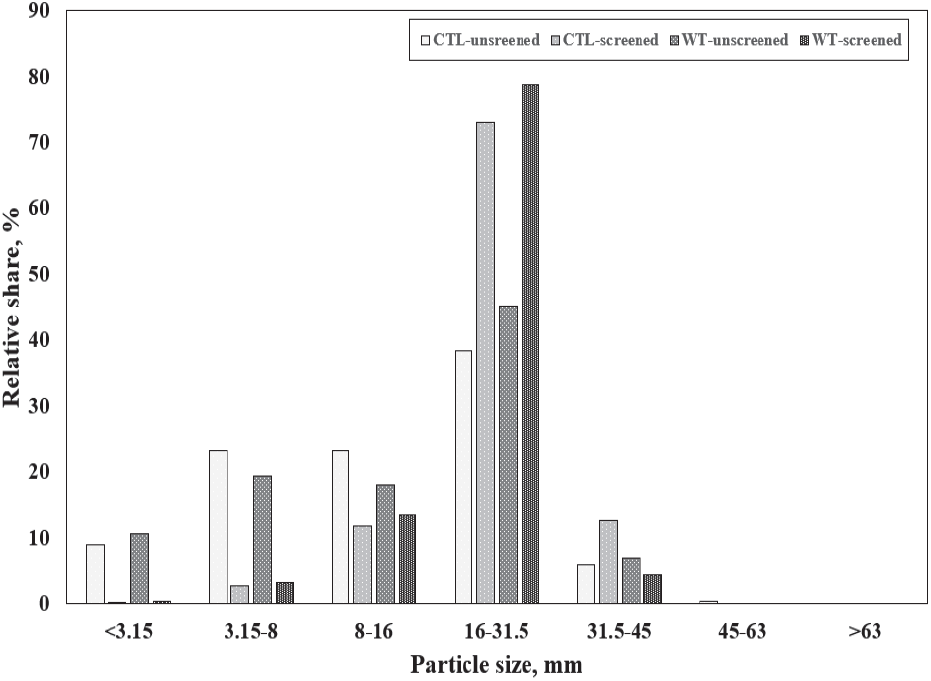
이는 Huber et al.(2017)의 연구결과에서 사용된 목재파쇄기와 선별기계의 스크린 형태가 다르지만 유사한 연구결과로 나타났다.
본 연구는 단목 및 전목수확시스템의 벌채부산물 목재칩 선별처리에 따른 미세분 차이 유의성을 검증하기 위해 t-검정을 실시한 결과 선별처리에 유의수준은 5%이내에서 통계적으로 유의한 차이가 있는 것으로 나타났다(Table 4).
또한 단목 및 전목수확시스템의 벌채부산물 목재칩 선별처리에 따른 미세분 크기 차이를 일원배치 분산분석을 실시한 결과 통계적으로 유의한 차이가 있는 것으로 나타났다(P<0.05). 이에 Duncan 사후검증을 실시한 결과 선별전 단목과 전목수확시스템의 벌채부산물 목재칩은 각각 다른 그룹으로 나타났고, 선별된 단목과 전목수확시스템의 벌채부산물 목재칩은 같은 그룹에 속하는 것으로 나타났다. 이는 선별처리에 따라 미세분이 감소된 효과로 판단된다(Figure 5).
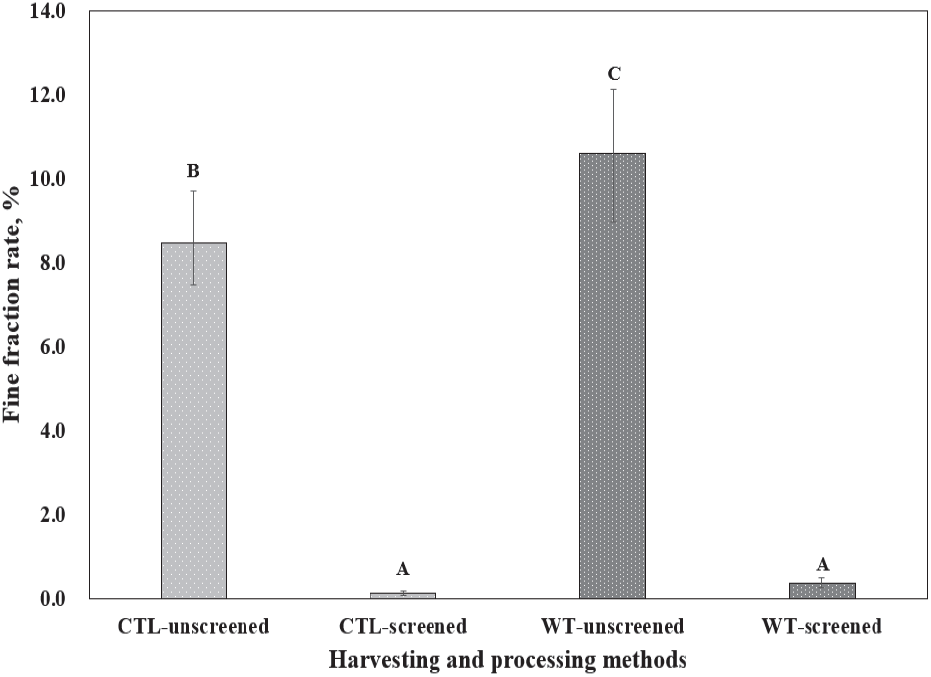
목재칩의 크기는 에너지 연료로 사용하는 바이오매스 보일러에 매우 중요한 인자로 크기가 증가할수록 연료공급 스크류의 과부하와 미세분 비율이 높을수록 불완전 연소로 문제가 발생 될 수 있다(Euh et al., 2014; Moskalik and Gendek, 2019). 이에 에너지 연료로 이용할 수 있는 시설에서 요구되는 목재칩 크기는 국제표준에서 P16S에서 P45S까지 등급을 분류하고, 국내기준에서는 P16S에서 P200까지 분류하고 있다. 본 연구에서는 단목수확시스템의 선별전후 목재칩에서 크기 등급은 P31S으로 나타났고, 전목수확시스템의 선별전 목재칩은 P31, F10, 선별후는 P31S로 나타났다. 이는 선별전 전목수확시스템 목재칩은 미세분 등급에 미치지 못하였지만 이를 제외한 선별전후 단목수확시스템과 선별후 전목수확시스템 목재칩은 에너지 이용 시설에 적합한 크기로 나타났다. 따라서 벌채부산물을 목재칩의 품질을 향상시킬 수 있는 선별처리를 통해 저급원료를 경제적이고, 품질이 높은 연료로 사용할 수 있을 것으로 판단된다.
겉보기 밀도는 국제표준에서 BD150, 200, 250 ≥ BD250 kg/m3까지를 A1 등급, BD150, 200, 250, 300 ≥ BD 300kg/m3까지를 A2 등급으로 분류하며, B 등급에서는 최소로 제시하면 된다. 국내기준은 1급이 ≥ 200kg/m3, 2급은 ≥ 150kg/m3으로 분류하고 있다. 함수율은 국제표준에서 A1 등급은 ≤ 25% in mass, A2 등급은 > 25 and ≤ 55% in mass으로 분류되며, 국내기준에서 1급은 M25 ≤ 25 w-%, 2급은 M35 ≤ 35 w-%으로 분류된다. 이를 바탕으로 목재칩의 겉보기 밀도 및 함수율 등급 분류 결과는 Table 5와 같다.
Harvesting methods | Wood chips | |||||
---|---|---|---|---|---|---|
Bulk density (kg/m3) | Grade | Moisture content (%) | Grade | |||
ISO 17225-4 (2014) | NIFoS, 2020 | ISO 17225-4 (2014) | NIFoS, 2020 | |||
CTL | 245.1 | A2 | First class | 22.9 | A1 | First class |
WT | 282.2 | A2 | First class | 34.1 | A2 | Second class |
단목과 전목수확시스템에서 생산된 벌채부산물 목재칩의 겉보기 밀도는 각각 A2와 1급, A2와 2급으로 분류되었다. 선행연구에서 목재칩의 겉보기 밀도는 원료(Raw material)와 함수율에 따라 차이가 있지만 최소 191 kg/m3에서 최대 488 kg/m3까지의 범위를 가진다(Nordhagen, 2014). 또한 겉보기 밀도는 운송작업에 영향을 미치며, Cho(2019)의 선행연구에서 함수율 30% 기준, 가공되지 않은 벌채부산물(167 kg/m3) 보다 목재칩(232 kg/m3)으로 운송작업하면 약 26.2%의 비용이 절감되는 것으로 보고하였다.
단목과 전목수확시스템에서 벌채부산물 목재칩의 함수율은 각각 A2와 1급, A2와 2급으로 분류되었다. Loria (2015)는 목재칩 함수율이 보일러나 열병합 발전 효율에 매우 중요한 인자로 함수율 45%에서 효율은 약 74%였으며, 함수율이 10∼15%로 낮아지면 효율은 최대 80%까지 높아지는 것으로 보고하였다. 또한 가스화 열병합 발전에 이용되는 목재칩의 기준은 함수율이 약 13% 미만으로 요구되었다(Pollex et al., 2020). 따라서 향후 에너지 이용시설에 따른 최적 함수율 조건을 만족하기 위해 벌채부산물의 저장 및 건조에 관한 연구가 필요할 것으로 사료된다.
단목 및 전목수확시스템의 벌채부산물 목재칩 선별처리에 따른 회분함량은 Table 6과 같다. 단목 및 전목수확시스템의 벌채부산물 목재칩 선별처리를 통해 회분함량이 낮아지는 것으로 나타났고, 선별전 목재칩은 단목수확시스템보다 전목수확시스템의 목재칩 회분함량이 낮은 것으로 나타났다. 이는 선별처리를 통해 미세분이 감소된 효과로 사료된다. 또한 선별된 단목수확시스템보다 전목수확시스템의 목재칩 회분이 낮은 원인은 수집과정에서 단목수확시스템은 굴삭기 우드그랩을 이용하여 벌채부산물를 지표면과 접촉하여 집재하기 때문에 토양과 이물질이 포함되어 전목수확시스템의 벌채부산물 목재칩 보다 높은 회분함량이 나타나는 것으로 판단된다. 이에 단목수확 및 전목수확시스템의 벌채부산물 목재칩 선별처리에 따른 회분함량 차이에 대한 유의성을 검증하기 위해 t-검정을 실시한 결과는 각 처리 간의 유의수준 5% 이내에서 통계적으로 유의한 차이가 있는 것으로 나타났다.
또한 단목 및 전목수확시스템의 벌채부산물 목재칩 회분함량 차이를 분석하기 위해 일원배치 분산분석을 실시한 결과 목재칩의 회분함량은 통계적으로 유의한 차이가 있는 것으로 나타났다(P<0.05). 또한, Duncan 사후검증을 실시한 결과 단목 및 전목수확시스템의 선별전후 목재칩은 각각 다른 그룹에 속하는 것으로 나타났다(Figure 6).
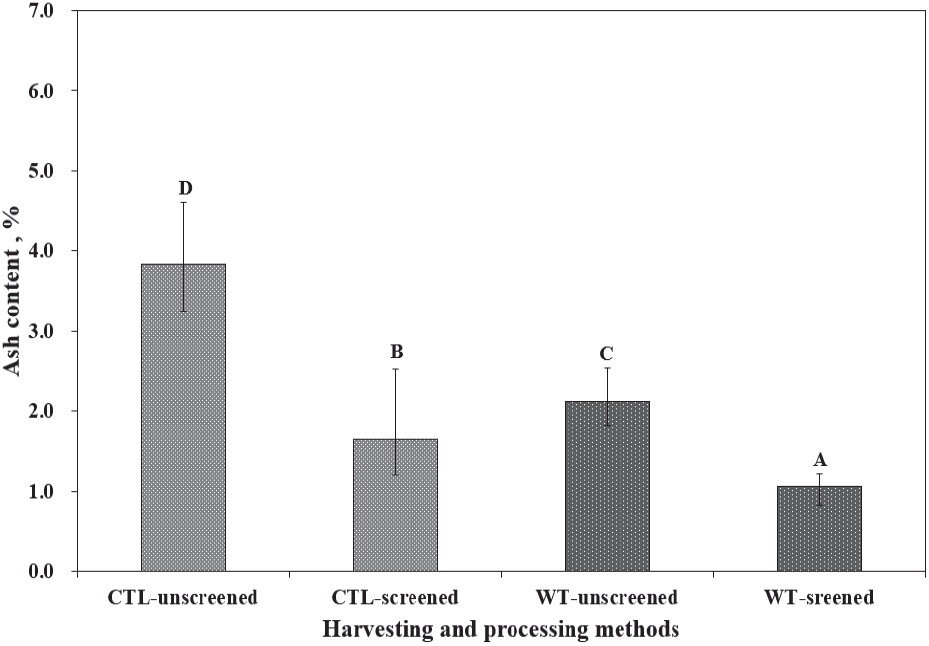
단목수확시스템에서 선별전후 목재칩은 회분함량이 각각 평균 3.84 w-% dry와 1.65 w-% dry로 57.0% 감소되었다. 전목수확시스템에서는 선별전후 목재칩은 회분함량 각각 평균 2.12 w-% dry와 1.06 w-% dry로 50.0% 감소되었다(Figure 8). 국제표준으로 전목수확시스템에서 선별된 목재칩만 A1 등급으로 분류되었고, 이를 제외한 목재칩은 등급에 분류되지 못하는 것으로 나타났다. 국내기준으로 단목수확시스템의 선별전 목재칩은 등급에 분류되지 못하였지만 선별처리를 통해 2급으로 개선되어 분류되었고, 전목수확시스템의 선별전 목재칩은 2급, 선별처리를 통해 1급으로 개선되어 분류되었다. Huber et al.(2017)의 선행연구에서 본 연구와의 선별장비와 스크린 형태는 다르지만 선별처리을 통해 회분함량이 감소되는 유사한 연구결과가 도출되었다. 따라서 벌채부산물의 회분함량은 수집과정, 수종 등에 따라 발생이 달라질 것으로 사료되며, 향후 추가적인 연구를 통해 회분함량을 감소 시킬 수 있는 수집시스템이 필요할 것으로 판단된다.
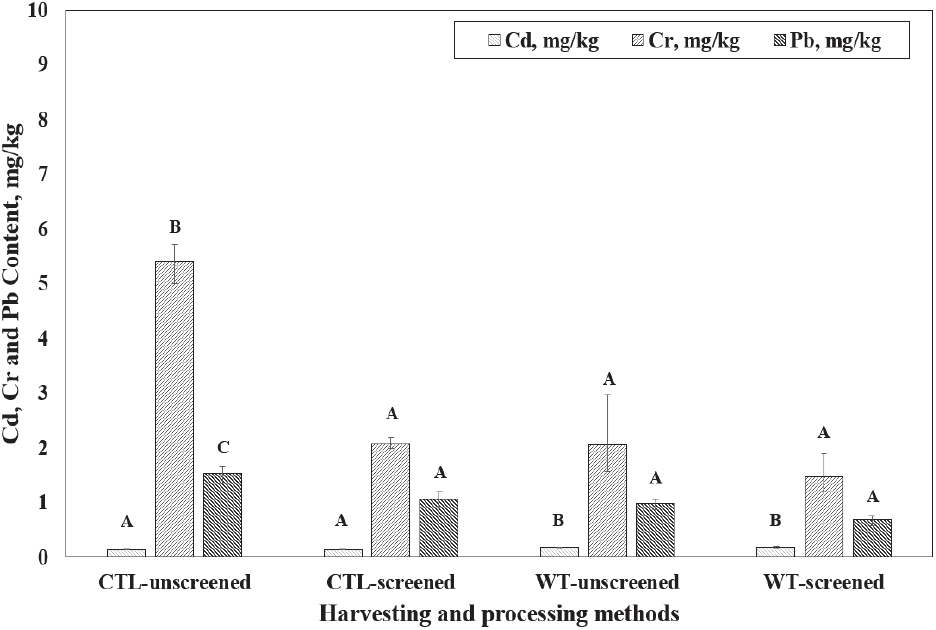
단목 및 전목수확시스템의 벌채부산물 목재칩 선별처리에 따른 질소, 황과 염소 함량에 따른 원소분석 결과는 Table 7과 같다. 염소함량의 경우 소량으로 검출되어 선별에 대한 차이가 없음을 판단하여 이를 제외하고 질소와 황 함량을 대상으로 분석을 실시하였다. 단목 및 전목수확시스템의 벌채부산물 목재칩을 각각 선별처리 유무에 따른 질소와 황 함량의 유의성을 검증하기 위해 t-검정을 실시한 결과 각 처리안에서 유의수준 5% 이내에서 통계적으로 유의한 차이가 있는 것으로 나타났으며, 이는 선별처리를 통해 미세분이 감소된 효과로 분석되었다.
Table 8과 같이 선별처리 유무에 따른 모든 목재칩에서 질소와 황 함량 차이를 분석하기 위해 일원배치 분산분석을 실시한 결과는 단목 및 전목수확시스템의 선별전후 목채칩에서 질소와 황 함량은 통계적으로 유의한 차이가 있는 것으로 나타났다(P<0.05).
Source | DF | Sum of squares | Mean squared | F-value | Prob>F |
---|---|---|---|---|---|
Nitrogen | 3 | 0.042 | 0.014 | 37.578 | 0.001 |
Sulfur | 3 | 0.005 | 0.002 | 29.398 | 0.001 |
또한, Duncan 사후검증을 실시한 결과 단목 및 전목수확시스템에서 선별전후 목재칩의 질소 함량은 각각 다른 그룹에 속하였고, 황 함량은 단목수확시스템의 선별전 목재칩을 제외한 모든 목재칩 동일한 그룹에 속하는 것으로 나타났다(Figure 7).
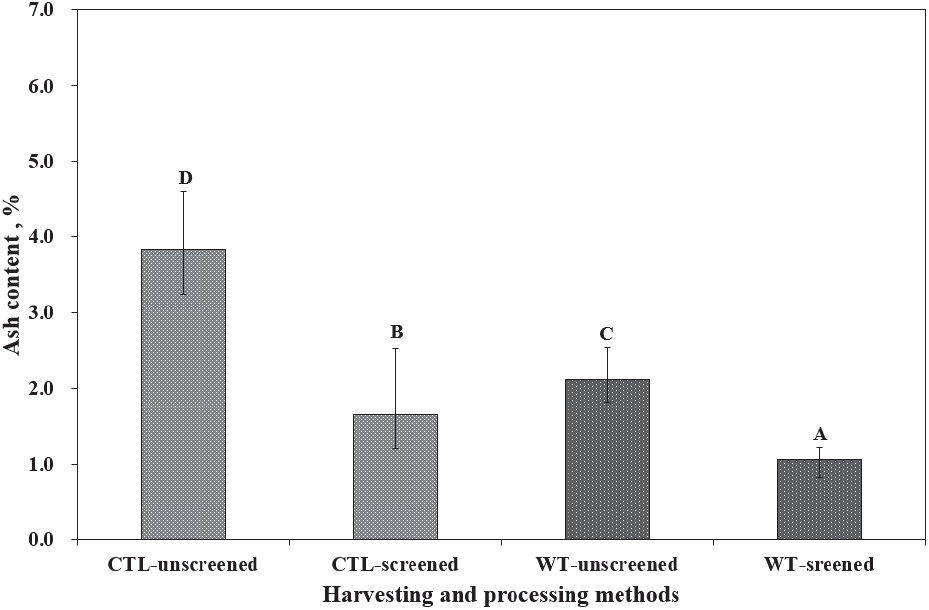
질소함량은 단목 선별전 목재칩에서 평균 4.6 w-%로 가장 높게 나타났으며, 선별처리를 통해 0.30 w-%로 93.5%로 감소되었고, 전목은 선별전 목재칩이 평균 0.38 w-%로 선별을 통해 0.34 w-%로 10.5%로 감소되는 것으로 나타났다. 황 함량은 단목 선별전 목재칩에서 평균 0.0689 w-%로 가장 높게 나타났고, 선별처리를 통해 0.0226 w-%로 67.2%로 감소되었고, 전목은 선별전 목재칩이 평균 0.0230 w-%로 선별을 통해 0.0197 w-%로 14.3%로 감소되는 것으로 분석되었다.
국제표준에서는 목재칩의 원료가 벌채부산물에 해당할 경우 A1과 A2 등급에서는 분류되지 않으며, 이하 저급 원료의 경우 B 등급으로 분류된다. 국내기준은 1급과 2급에서 질소와 황 함량은 각각 ≤ 1.0 w-% dry, ≤ 0.1 w-% dry등급으로 분류된다. 본 연구의 벌채부산물 목재칩은 국제표준에서 등급 분류를 하지 않으며, 국내기준은 단목 및 전목수확시스템의 벌채부산물 목재칩은 등급에 모두 만족하는 것으로 나타났다. 벌채부산물로 생산된 목재칩의 경우는 품질 등급에 질소 함량이 반드시 언급되어야 한다고 보고하였다(Filippou et al., 2018). 또한 Pollex et al.(2020)은 토양오염에 대한 연료 지수인 Fe/Mn과 AI/200을 이용하여 벌채부산물 원료를 생산하는 과정에서의 토양오염이 연료에 영향을 미치는 것으로 보고하였다. 질소 및 황 함량은 벌채부산물를 수집하는 과정에서 토양 및 이물질 등에 영향을 많이 받게 되지만 등급 기준에서 제시된 원료의 형태를 가지는 벌채부산물에 경우에는 등급에 모두 만족되었고, 목재칩의 선별처리를 통해 질소와 황 함량이 감소됨으로써 목재칩의 품질이 더욱 향상될 수 있을 것으로 판단된다.
단목 및 전목수확시스템의 벌채부산물 목재칩 선별처리에 따른 비소, 카드뮴, 크롬, 납, 수은 등 무기물 분석결과는 Table 9와 같다. 그러나 비소와 수은은 검출되지 않아 이를 제외한 카드뮴, 크롬, 납을 대상으로 분석하였다. 단목 및 전목수확시스템의 벌채부산물 목재칩을 각각 선별처리 유무에 따른 카드뮴, 크롬과 납 무기물의 유의성을 검증하기 위해 t-검정을 실시한 결과 각 처리안에서 카드뮴과 납은 선별전후 목재칩에서 유의한 차이가 없었고, 크롬은 단목수확시스템의 선별전후에 목재칩은 5% 이내에서 통계적으로 유의한 차이가 있었으며, 전목수확시스템의 선별전후 목재칩은 유의한 차이가 없는 것으로 나타났다. 이는 Table 10과 같이 선별처리 유무에 따른 모든 목재칩에서 카드뮴, 크롬과 납 함량 차이를 분석하기 위해 일원배치 분산분석을 실시한 결과는 단목 및 전목수확시스템의 선별전후 목재칩에서 카드뮴, 크롬과 납 함량은 통계적으로 유의한 차이가 있는 것으로 나타났다(P<0.05).
Source | DF | Sum of squares | Mean squared | F-value | Prob>F |
---|---|---|---|---|---|
As | 3 | 0.003 | 0.001 | 10.462 | 0.004 |
Cd | 3 | 28.932 | 9.644 | 42.124 | 0.001 |
Cr | 3 | 1.143 | 0.381 | 22.508 | 0.001 |
또한, Duncan 사후검증을 실시한 결과 카드뮴은 단목 및 전목수확시스템의 선별전후 목재칩은 각각 같은 그룹으로 속하였고, 크롬과 납 함량은 단목수확시스템의 선별전 목재칩을 제외한 단목수확시스템 선별후, 전목수확시스템의 선별전후 목재칩이 동일한 그룹에 속하는 것으로 나타났다(Figure 8).
카드뮴 함량은 단목 선별전후가 평균 0.141 mg/kg dry와 0.135 mg/kg dry로 4.3% 감소되었고, 전목 선별전후는 평균 0.178 mg/kg dry와 0.175 mg/kg dry로 1.7% 감소된 것으로 나타났다. 크롬 함량은 단목 선별전후 평균 5.405 mg/kg dry와 2.069 mg/kg dry로 61.7% 감소되었고, 전목 선별전후는 평균 2.052 mg/kg dry와 1.470 mg/kg로 28.4%로 감소되었다. 납 함량은 단목 선별전후가 평균 1.540 mg/kg dry와 1.058 mg/kg dry로 31.3% 감소되었고, 전목 선별전후는 평균 0.978 mg/kg dry와 0.677 mg/kg dry로 30.8% 감소되는 것으로 분석되었다. 이는 모든 목재칩에서 선별처리를 통해 각각 함량이 감소된 것으로 나타났고, 무기물의 경우 탄소(Carbon)를 포함하지 않은 양분으로 가열해도 타지 않고 변화도 없기 때문에 토양과 이물질이 더 포함된 목재칩의 경우 연소 시 문제가 될 가능성이 크다. 국제표준에 따르면 무기물은 원소분석과 동일하게 원료를 벌채부산물로 생산한 목재칩에서는 등급에 해당되지 않는다. 국내기준은 1급과 2급에서 카드뮴은 ≤ 1.0 mg/kg dry, 크롬과 납은 ≤ 1.0 mg/kg dry으로 분류되고, 이에 따르면 모두 1급, 2급에 해당되는 것으로 나타났고, 모든 무기물 항목에 만족하는 것으로 분석되었다. Pollex et al.(2020)의 연구에서도 선별처리을 통해 목재칩 회분 함량과 미세분 비율을 감소시킬 뿐만 아니라 화학 원소 함량까지 감소시키는 결과로 본 연구결과와 유사한 것으로 나타났다. 따라서 원료를 벌채부산물 대상으로 생산한 목재칩을 에너지 연료로 사용함에 있어 문제가 없을 것으로 판단된다.
단목 및 전목수확시스템의 벌채부산물 목재칩 선별처리에 따른 발열량 분석결과는 Table 11과 같다. 분석결과 선별처리를 통해 단목 및 전목수확시스템의 벌채부산물 목재칩 모두 발열량이 증가하는 경향이 나타났으며, 선별처리를 통한 단목수확시스템의 목재칩 발열량이 평균 18.48 MJ/kg와 전목수확시스템의 목재칩 발열량이 18.59 MJ/kg으로 각각 2.72%와 5.81% 증가한 것으로 나타났다. 또한 단목 및 전목수확시스템의 벌채부산물 목재칩 선별처리에 따른 발열량 차이에 유의성을 검증하기 위해 t-검정을 실시한 결과는 각 처리 간의 유의수준 5% 이내에서 통계적으로 유의한 차이가 있는 것으로 나타났다.
단목 및 전목수확시스템의 벌채부산물 목재칩의 발열량 차이를 분석하기 위해 일원배치 분산분석을 실시한 결과 발열량은 통계적으로 유의한 차이가 있는 것으로 나타났다(p<0.05). 또한, Duncan 사후검증을 실시한 결과 단목과 전목에서 처리된 미선별 및 선별 목재칩은 각각 다른 그룹에 속하는 것으로 나타났다(Figure 9).
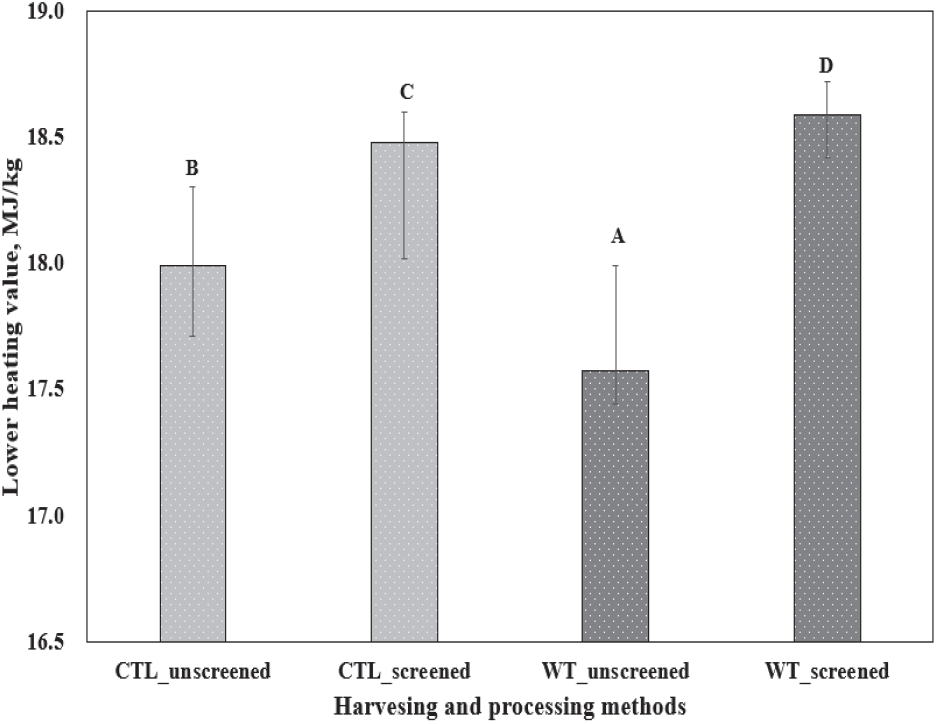
일반적으로 목질 연료의 발열량은 함수율이 낮을수록 높아지는 것으로 알려져 있으며(Abe, 1986; Kang et al., 2008), 목재칩 발열량에 미치는 가장 큰 인자로 회분이 1% 증가되면 발열량이 약 0.11 MJ/kg 감소되는 것으로 보고하였고(Lieskovsky et al., 2017), 회분함량과 발열량에 선형관계에 따라 회분함량이 감소할수록 발열량이 증가된다고 보고하였다(Gendek et al., 2018). 본 연구에서도 단목 및 전목수확시스템의 벌채부산물 목재칩 선별처리에 따라 발열량이 증가되었으나 그 차이는 크기 않았으며(Figure 9), Huber et al.(2017)의 연구 결과에서도 오히려 선별후 목재칩의 발열량이 가장 낮았지만, 선별전 목재칩과 크게 다르지 않는 것으로 보고하였다. 그러나 국제표준과 국내기준에서 동일하게 발열량은 최소로 낼 수 있는 열량만을 표시하게 되어 있으며, 등급으로 분류가 되어있지 않다. 그러나 함수율과 회분함량에 따른 발열량 변화로 목재칩을 연료로 이용하는 보일러나 열병합 발전시스템 효율에 저하 등에 원인에 문제가 될수 있어 공급되는 목재칩 발열량의 품질 등급 분류가 필요할 것으로 판단된다.
단목 및 전목수확시스템과 벌채부산물 목재칩의 가공처리에 따른 품질 등급 분류를 통해 에너지 연료로 사용하는 이용시설에 최종 공급 비용과 이용 가능성을 분석하고자 하였다. Table 12는 단목 및 전목수확시스템의 벌채부산물 목재칩을 국제표준과 국내기준으로 구분하여 등급 분류한 결과이다. 단목수확시스템에서 생산된 목재칩은 국제표준과 국내기준에 적합하지 않았고, 선별처리를 통해 국제표준은 A2 등급과 국내기준 2급에 해당하여 등급이 향상된 것으로 나타났다. 전목수확시스템의 선별전 목재칩은 국제표준에 해당되지 않았고, 국내기준에서 2급으로 나타났다. 또한 선별처리를 통해 국제표준 A2 등급으로 향상되었고, 국내기준 동일한 2급으로 나타났다.
Harvesting and processing methods | ||||||||
---|---|---|---|---|---|---|---|---|
Property class | CTL-unscreened | CTL-screened | WT-unscreened | WT-screened | ||||
ISO 17225-4 (2021) | NIFoS (2020) | ISO 17225-4 (2021) | NIFoS (2020) | ISO 17225-4 (2021) | NIFoS (2020) | ISO 17225-4 (2021) | NIFoS (2020) | |
Origin and source | forest biomass | |||||||
Particle size | P31S | P31S | P31, F10 | P31S | ||||
Moisture | A1 | First class | A1 | First class | A2 | Second class | A2 | Second class |
Ash | n.a.a | n.a.a | n.a.a | Second class | n.a.a | Second class | A1 | First class |
Bulk density | A2 | First class | A2 | First class | A2 | First class | A2 | First class |
Elemental (N, S and Cl) | n.a.b | First class | n.a.b | First class | n.a.b | First class | n.a.b | First class |
Inorganic substance (As, Cd, Cr, Pb and Hg) | n.a.b | First class | n.a.b | First class | n.a.b | First class | n.a.b | First class |
Final class | n.a.a | n.a.a | A2 | Second class | n.a.a | Second class | A2 | Second class |
앞서 서론에서 언급한 것으로 국내는 벌채부산물을 이용한 에너지 이용시설를 확대하고 있다. Figure 10은 단목 및 전목수확시스템의 벌채부산물로 생산된 목재칩을 생산 및 가공처리에 따른 등급 분류를 통해 최종적으로 이용할 수 있는 4가지 이용시설(Biomass gasification CHP(Combined Heat and Power) system, ORC(Organic Rankine Cycle) based biomass-fired CHP system, Steam turbine-based biomass-fired CHP system, Biomass-fired boiler system)를 고려하여 경제적인 이용 가능성을 검토하였다. Plant A의 경우 목재칩을 가스화하여 열 및 전기를 생산하는 열병합발전 시스템이다. 이 시스템(Spanner Re2 GmbH)에서 요구되는 목재칩은 국제표준의 원료 형태(Origin and source)와 목재칩 크기(P16S)에 따라 B2 등급 까지 이용가능하지만, 일반적인 연소시설 보다 낮은 함수율(13% 미만)이 요구된다. 따라서 함수율 조건을 만족하기 위해서는 건조처리가 필수적이다. 건조비용은 선행연구 Raitia and heiskane (2015)에서 제시한 12,650 won/m3을 톤으로 환산한 42,204 won/ton (300kg/m3 기준)을 적용하였다. 이에 Plant A에서는 단목수확시스템의 선별전 목재칩을 제외한 모든 목재칩이 이용가능하였고, 건조처리 비용을 추가한 전목수확시스템의 선별전 목재칩이 99,408원/톤으로 가장 경제적이였다. Plant B, C, D의 경우 목재칩을 연료로 사용하는 보일러가 기본이 되며, 투입되는 목재칩 품질에 따라 효율이 변화하고 가스화 열병합 발전시스템보다 높은 함수율도 연소할 수 있다. 이는 Plant A와 같이 낮은 함수율이 요구되지 않아 건조비용은 추가적으로 필요하진 않지만 효율을 위해서는 함수율 관리가 필요하다. 목재칩 보일러에서 요구되는 목재칩 크기는 국제표준에서 분류된 P45S 범위 안에 속하면 이용 가능하다. 이를 기반으로 Plant B, C, D에서는 Plant A에서와 같이 단목수확시스템의 선별전 목재칩을 제외한 모든 목재칩이 이용 가능하고 전목수확시스템의 선별전 목재칩이 57,204 won/Gwt으로 가장 경제적으로 이용할 수 있을 것으로 판단된다. 본 연구는 에너지 이용시설로 가장 적합하고 경제적으로 이용할 수 있는 에너지 연료인 전목수확시스템의 선별전 목재칩이 가장 유리한 것으로 나타났다. 국내는 대부분 단목수확시스템을 이용하여 목재를 수확하기 때문에 원료의 품질 저하와 높은 비용이 요구되지만 추가적인 처리(선별, 건조)를 통해 연료의 품질이 향상됨으로 에너지로 이용할 수 있음을 확인하였다. 그러나 국내는 2020년 이전에 연료용 목재칩에 대한 등급 분류가 없었으나, 이를 기점으로 목재칩 등급을 강화하고 분류함으로써 국제표준에서 분류한 등급에 도달할 수 있도록 노력하고 있다. 따라서 에너지를 이용하는 시설에서 요구되는 목재칩을 생산하기 위해서는 목재수확방법을 고려한 목재칩 생산이 매우 중요하며, Figure 10에서 제시한 기준을 활용하여 목재칩의 고품질화와 가장 경제적으로 생산하여 공급하기 위한 의사결정 자료로 활용할 수 있을 것으로 판단된다.
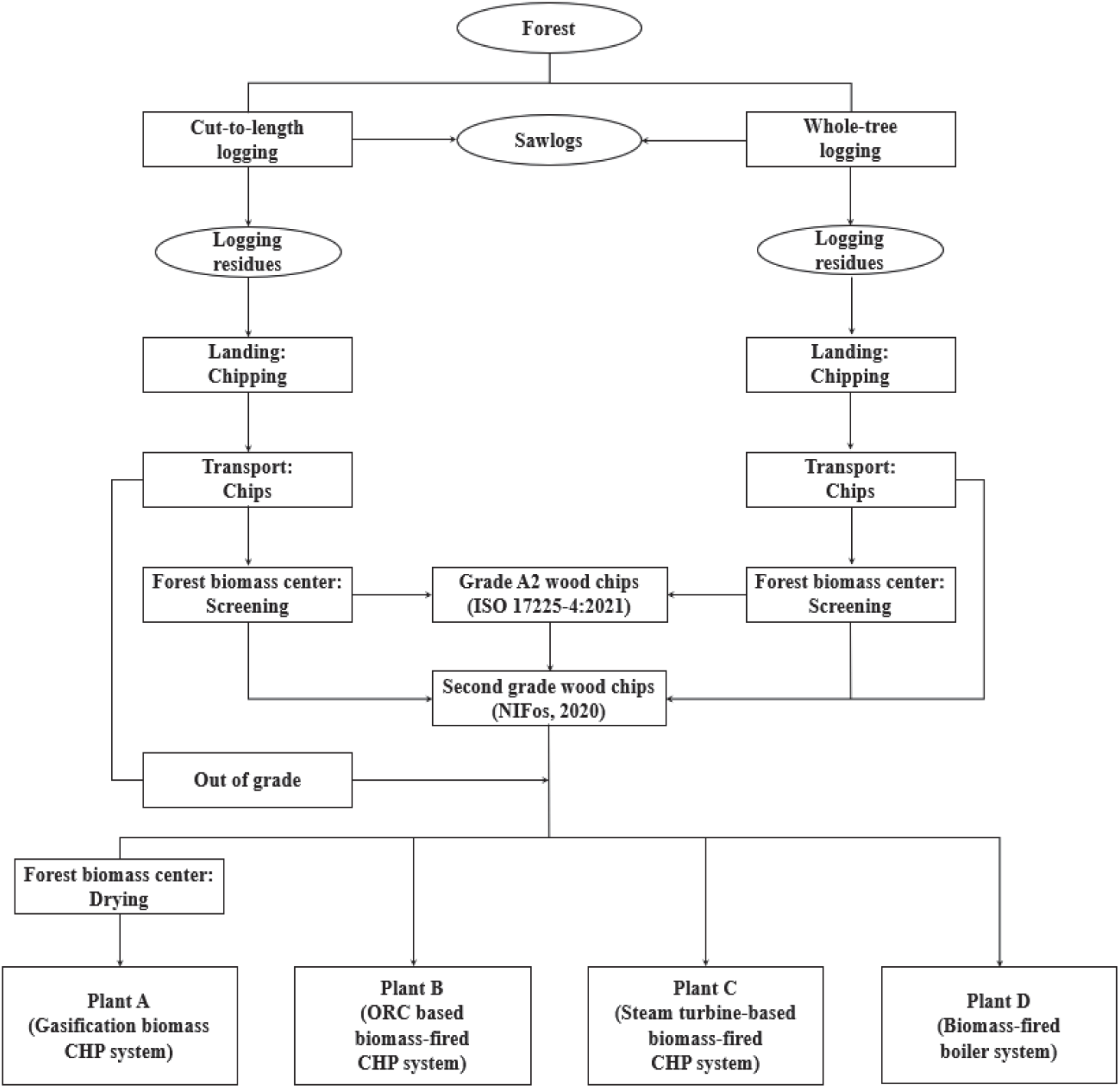
결 론
전 세계적으로 증가하는 에너지 수요와 화석 연료의 온실가스 배출 증가에 따른 부정적 영향에 대한 우려로 이를 대체할 수 있는 벌채부산물은 친환경적이고, 재생 가능한 에너지원이다. 따라서 본 연구에서는 목재수확방법별 벌채부산물 목재칩의 생산·가공에서 생산성 및 비용, 생산된 연료용 목재칩 연료 특성과 등급 분류를 분석하여 에너지 이용시설에서의 적합성과 이용 가능성을 검토하고자 하였다. 단목수확시스템에서 전목수확시스템으로 적용하면 생산성이 향상되어 저비용으로 벌채부산물 목재칩 생산이 가능하였다. 그러나 단목수확시스템에서 생산된 목재칩은 연료로써 적합하지 않았고 선별처리를 통해 목재칩을 연료로 이용할 수 있을 것으로 나타났다. 또한 에너지 이용시설를 고려한 목재칩 생산 및 공급은 연료 등급 분류에 적합하고 비용적으로 가장 낮은 전목수확시스템의 목재칩을 이용하는 것이 가장 경제적일 것으로 판단된다. 향후 목재수확방법별 다양한 수종과 조건 등을 고려한 벌채부산물 목재칩의 등급 분류를 통해 에너지 이용시설에서 연소 후 발생되는 연소가스, 미세먼지 등이 환경적으로 미치는 영향에 대한 검토와 추가적인 연구가 진행되어야 할 것으로 사료된다.